一、定义阶段
1.项目背景
VOB:随着公司业务增长,作业量增加,加班多,订单不均衡,作业量不均衡,仓储人力资源不能充分利用。
VOC:仓储作业订单不均衡,时多时少,造成有时加班,有时空闲;产品类型差异大,订单作业时间有长有短;作业过程中等待时间长,导致订单完成时间长。
2.问题描述
a.2014年1-9月分入库和出库单数及件数。以月为单位分类统计,月度作业量不均衡。
b. 以2014年5-7月份为例,以日为单位分类统计。每日作业量不均衡。
3.CTQ树分析
关键CTQ为:人均小时单数,可以分解成:仓储作业标准工时和作业效率(OPE)。
4.指标定义
指标类型定义:单位时间内完成的货物的出、入库单数。
Y1=仓储作业标准工时
入库:30分/单* X1(非辛迪思产品的单数)+80分/单* X2(辛迪思产品单数)
【注:入库工时=系统操作+打印单据+拣配+复核+上架+过账】
出库:25分/单* X1(非辛迪思产品的单数)+60分/单* X2(辛迪思产品单数)
【注:出库工时=系统操作+打印单据+拣配+复核+过账+顺丰单+打包+核对信息】
Y2=作业效率(OPE)=作业量(单数)*标准工时/工作时间
5.项目范围
a.收货
关键过程为:采购下单——到货验收——出具验收单——录入、打单——入库、上架
SIPOC图如下:
b.发货
关键过程为:接单——拣货出库——物流配送——客户收货——反馈
SIPOC图如下:
6.项目目标及收益
a.项目目标
·标准工时由目前的入库每单110分钟(辛迪思和其他)减少为95分钟,降低13.6%;出库每单85分钟减少为70分钟,降低17.6%;
·OPE由当前的0.57提升到0.67,提高17.5%。
b.项目收益
节省人力成本=人数*15%*人力成本=24*15%*7万≈21万
7.项目计划
二、测量阶段
1.测量系统分析
·作业量统计:基于 SAP系统,可以按日统计。
·作业时间:出勤记录,手工记录与指纹考勤一致;通过录像和宽放抽样得到并验证了作业的标准工时。
2.作业标准工时表
根据录像分析,得到了当前的基准标准工时表:
3.岗位直接作业的OPE
a.引入OPE
为了更客观的反应单位劳动时间产生的工时量,引入OPE的概念,它能规避劳动减员造成的干涉,同时以OPE为指标也符合公司14年对库房人员基数进行控制的意识导向。
OPE=作业时间/工作时间,(作业时间=作业量×标准工时)
b.直接直接作业工作量统计
c.作业时间分布
用宽放抽样的方法来发现问题,分析原因。整个作业的过程中包含辅助作业的时间,例如:业务沟通、项目开会,系统测试等。除了直接作业和辅助作业以外,个人的饮水、去卫生间等均纳入到休息时间。
三、分析阶段
通过分析发现,影响仓储作业效率的因素有很多。对这些因素从严重性、频次以及对业务的影响等维度综合考虑,决定对占主要影响的问题优先改进。
四、改进阶段
a.改进机会1:分析现有标准工时,减少标准作业环节,降低作业时间,从而降低标准工时。
b.改进机会2:通过5S定制管理提升工作效率。
c.改进机会3:提高辅助作业的效率
·加强与部门之间的衔接沟通,降低等待时间。
单向沟通设定反馈时间机制。多向沟通由运管部牵头开现场会,第一时间讨论、解决。
·熟练操作SAP系统,定期进行系统培训。
·WMS系统优化后入库对比
d.小时作业量分析及人力改善方案
通过数据收集,可以得出:
·早上8:30上班,9点前基本做5s,单据比较少。
·上午9点-11点订单较少。
·2-4点效率最高。其中2-3点批量入库,4-5点集中出库。
根据数据分析,可以制定以下方案:
五、控制阶段
1.SOP流程图的梳理及培训,包含30个流程,6个制度,4个办法及规定。
2.WMS系统上线。
3.员工内部培训:六西格玛仓储资源优化和配送资源优化的培训。
4.OPE的数据来源、审核流程及月度追踪。
1.项目背景
VOB:随着公司业务增长,作业量增加,加班多,订单不均衡,作业量不均衡,仓储人力资源不能充分利用。
VOC:仓储作业订单不均衡,时多时少,造成有时加班,有时空闲;产品类型差异大,订单作业时间有长有短;作业过程中等待时间长,导致订单完成时间长。
2.问题描述
a.2014年1-9月分入库和出库单数及件数。以月为单位分类统计,月度作业量不均衡。
b. 以2014年5-7月份为例,以日为单位分类统计。每日作业量不均衡。
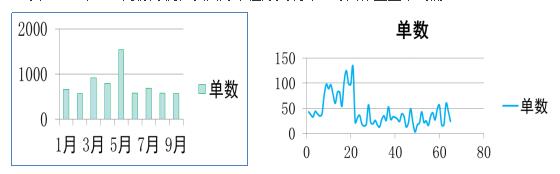
关键CTQ为:人均小时单数,可以分解成:仓储作业标准工时和作业效率(OPE)。
4.指标定义
指标类型定义:单位时间内完成的货物的出、入库单数。
Y1=仓储作业标准工时
入库:30分/单* X1(非辛迪思产品的单数)+80分/单* X2(辛迪思产品单数)
【注:入库工时=系统操作+打印单据+拣配+复核+上架+过账】
出库:25分/单* X1(非辛迪思产品的单数)+60分/单* X2(辛迪思产品单数)
【注:出库工时=系统操作+打印单据+拣配+复核+过账+顺丰单+打包+核对信息】
Y2=作业效率(OPE)=作业量(单数)*标准工时/工作时间
5.项目范围
a.收货
关键过程为:采购下单——到货验收——出具验收单——录入、打单——入库、上架
SIPOC图如下:

关键过程为:接单——拣货出库——物流配送——客户收货——反馈
SIPOC图如下:
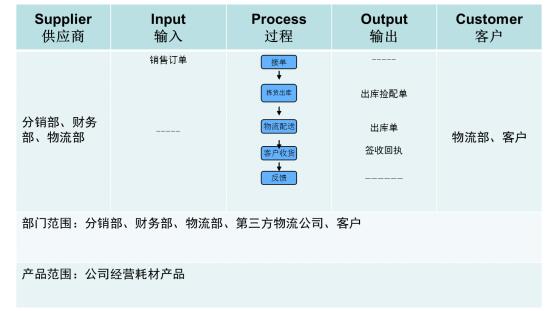
a.项目目标
·标准工时由目前的入库每单110分钟(辛迪思和其他)减少为95分钟,降低13.6%;出库每单85分钟减少为70分钟,降低17.6%;
·OPE由当前的0.57提升到0.67,提高17.5%。
b.项目收益
节省人力成本=人数*15%*人力成本=24*15%*7万≈21万
7.项目计划

1.测量系统分析
·作业量统计:基于 SAP系统,可以按日统计。
·作业时间:出勤记录,手工记录与指纹考勤一致;通过录像和宽放抽样得到并验证了作业的标准工时。
2.作业标准工时表
根据录像分析,得到了当前的基准标准工时表:
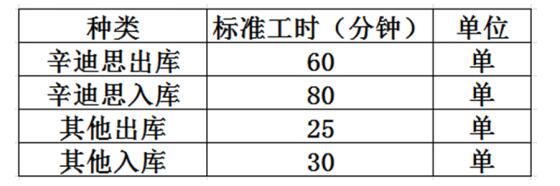
a.引入OPE
为了更客观的反应单位劳动时间产生的工时量,引入OPE的概念,它能规避劳动减员造成的干涉,同时以OPE为指标也符合公司14年对库房人员基数进行控制的意识导向。
OPE=作业时间/工作时间,(作业时间=作业量×标准工时)
b.直接直接作业工作量统计
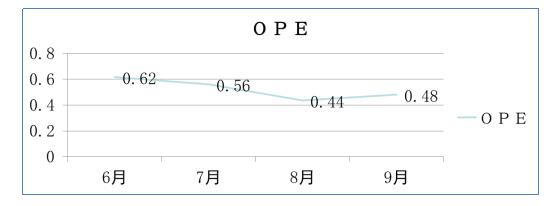
用宽放抽样的方法来发现问题,分析原因。整个作业的过程中包含辅助作业的时间,例如:业务沟通、项目开会,系统测试等。除了直接作业和辅助作业以外,个人的饮水、去卫生间等均纳入到休息时间。

通过分析发现,影响仓储作业效率的因素有很多。对这些因素从严重性、频次以及对业务的影响等维度综合考虑,决定对占主要影响的问题优先改进。
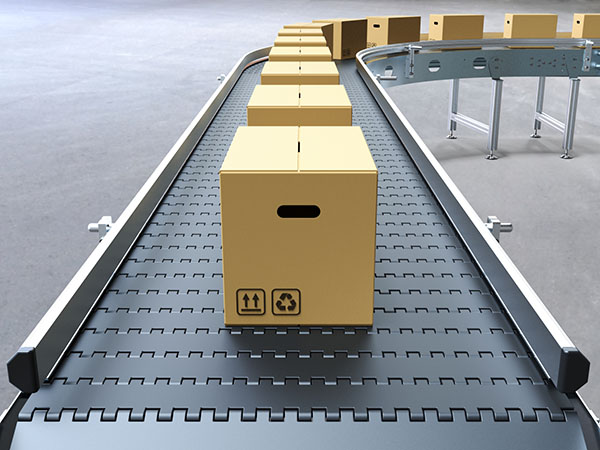
a.改进机会1:分析现有标准工时,减少标准作业环节,降低作业时间,从而降低标准工时。

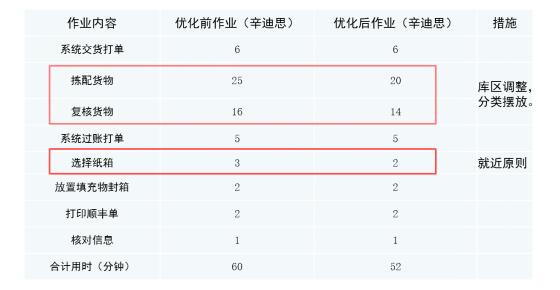
·加强与部门之间的衔接沟通,降低等待时间。
单向沟通设定反馈时间机制。多向沟通由运管部牵头开现场会,第一时间讨论、解决。
·熟练操作SAP系统,定期进行系统培训。
·WMS系统优化后入库对比
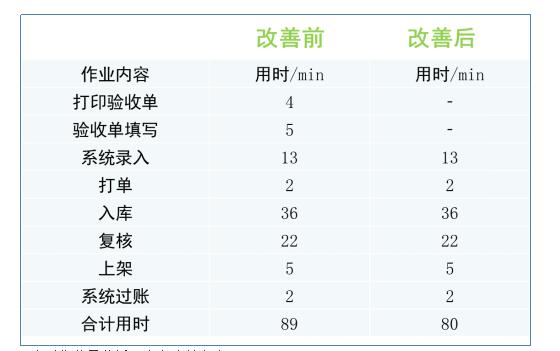
通过数据收集,可以得出:
·早上8:30上班,9点前基本做5s,单据比较少。
·上午9点-11点订单较少。
·2-4点效率最高。其中2-3点批量入库,4-5点集中出库。
根据数据分析,可以制定以下方案:
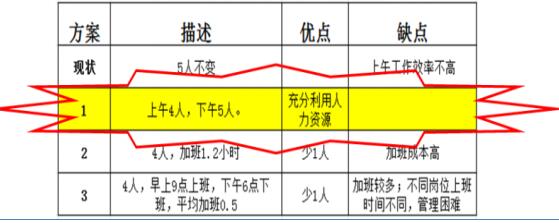
1.SOP流程图的梳理及培训,包含30个流程,6个制度,4个办法及规定。
2.WMS系统上线。
3.员工内部培训:六西格玛仓储资源优化和配送资源优化的培训。
4.OPE的数据来源、审核流程及月度追踪。
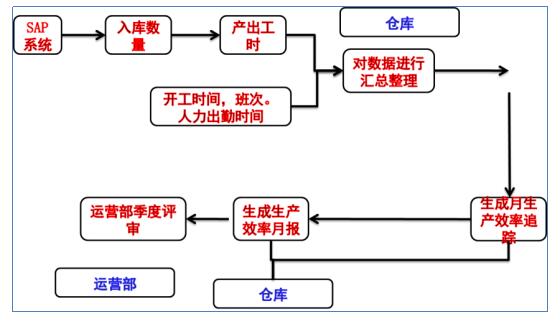
作者:博革咨询
推荐新闻
苏州矿山机械领军企业精益改善优秀成果展现
博革于2021年10月正式与苏州创力达成合作,签署精益布局项目,旨在全面改造升级齿轮车间,历时4个月完成前期规划,另根据规划项目历时1年改造完成,现新车间已经投入使用,并且达到预期目标。 /news/4855.html
博革携手江东金具设备制造,精益咨询管理改善促生产
江东金具决定与上海博革咨询达成协议:由上海博革咨询为江东金具进行工厂布局规划和目视化设计工作。项目定位为打造绝缘子行业国内领先、行业标杆的智能化、自动化灯塔工厂。 /news/4866.html
国内PPE行业领军企业赛立特园区精益布局
博革自2022年起为赛立特提供精益管理服务,助力企业搭建精益管理体系,推动精益化管理落地见效,从而全面转型升级,提升企业竞争力。本次项目从2024年10月进驻,经过调研分析,围绕园区整布局 /news/4864.html